 |
 |
(1) |
従来の経営/組織運営の課題 |
|
日本の今日の工業経済を支えた原動力は、第2次世界大戦で荒廃した日本の戦後復興において、欧米並みの豊富な“物”の容易な取得でありました。
「欧米に追いつき、追越せ」が国民的目標で、日本の企業が主体となって邁進しました。 世界の先端を切って民生レベルの「品質管理」の浸透と日本人の特徴であった勤勉と立地条件が相俟って「高品質」の製品を世界に送り出し、貿易立国として成功しました。 日本式生産方式も同時に世界に進出を果たしました。工業製品は世界的に共通化してきました。同様な生産手段は世界の至るところに構築され、物不足は解消されつつあります。
21世紀は「大量生産」や「増収・増益」の20世紀型の経営はもはや成り立たなくなりつつあります。日本の工業製品は国際的に“A級”の認識が確立しています。「高級品」の品質水準が確立されれば、必ずしも“A級”品に拘る必要のない状況が発想され、“B級”品ビジネスの存在も発生
しています。21世紀型のビジネスには「大量生産型」、「増収・増益 型」からターゲットを「品質レベル」を明確に意識(高級化志向に限定しない)
した経営コンセプトが求められています。
そのために必要なことは、“曖昧”、“About”、“成り行き”、“勘と経験”等の不確定なマネージメントを排して、経営指標、手段、原理、技術、人、設備、顧客ニーズ、“不具合”解析等に定量的なマネージメントを導入することであります。
20世紀型の経営の失敗と成功をベースに幣所が開発した「数量化マネージメント手法」;“QAMM”は各位の21世紀型の経営ニーズにお応えします。
|
|
 |
 |
(2) |
“QAMM”の展開基本 |
|
従来の経営の“不具合”や改善は、ややもするとボトムアップ方式が採用されたり、出来合いの“改善システム”が導入された「全員参画」型が適用されています。例えこの結果が成功したとしてもその組織体“世間並み”になっただけです。 “不具合”の取り扱いも「どうしたら良いか?」
を誰かの責任の追及を覆った議論が普通化しています。これでは真の“不具合”の改善策に確実に到達することは稀にしかありません。多くの場合、経営資源の無駄使いをしています。
“QAMM”の展開の基本は大きく分けて3点に集約します。
(1)“不具合”は経営方針/事業方針(マネージメント)の“何”を阻害をしているか?
(2)“不具合”を「現象」として捉えます(人のやっていることも「現象」とします)
(3)改善は「制御」と定義します。
何故なら、人が“不具合”と感じること「自然現象」として捉え、解消するのではなく“不具合”につながらないように「制御」します。
例えば“落ちる”、は地球上の絶対的自然条件です。 落ちる原因の「万有引力」は解消できません。 “落ちる”ことによって起こる壊れや変形を、材料を強くしたり、壊れるまでの落下エネルギーが生じないように“落ち”ないようにしたり、途中で受け止めることで「制御」できます。方法の選択はコスト(実施の難儀さも含む)の指標で選択します。
改善の最終判断マネージメントされた「技術」が確実反映されることです。
“QAMM”は“不具合”やテーマに熟知した特定の少数(精鋭)者の活動で実践できることが特長です。
|
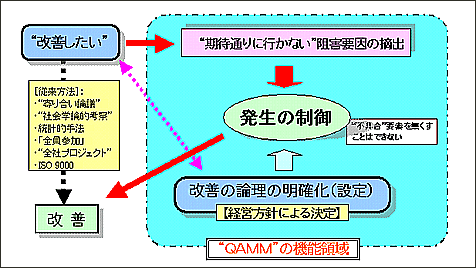
<図をクリックすると拡大表示します> |
“QAMM”のツール :
[“不具合”収集] [“不具合”解析] [“発生源解析”] [“全数確認技術”]
[“複合起因解析”] [“1%理論”] [発生確率防御設計] [量子力学論]
>>> "QAMM"のツールの説明
|
|
 |
 |
(3) |
“QAMM”の基本論理 |
|
製品や方法には必ず自然界の「原理」、「原則」が巧みに組み合わされた「論理」が適用されています。
その際、「原理」「原則」に間違った理解や自然現象を度外視した“人”の「思惑」設定があると“不具合”が発生します。
“QAMM”は目的に沿っているかどうかのプロセスの“不具合”発見と間違いを起こさない論理設定と「原理」「原則」の的確な適用を点検するシステムです。
 |
 |
【原理】; |
人間にはどうにもならない自然界に存在する現象
例;引力、位置エネルギー、熱現象、静電磁力 |
【原則】; |
自然現象を人間が共通に理解できるように整理、整頓した約束事 |
【論理】; |
原理・原則を巧みに組み合わせ、人間に有益な「装置、物」を作り上げること |
※人間の作った「装置、物」を正しく知ろうとするには、(1)論理を知り、(2)使われている原理・原則の適用に立ち入る必要がある。 |
|
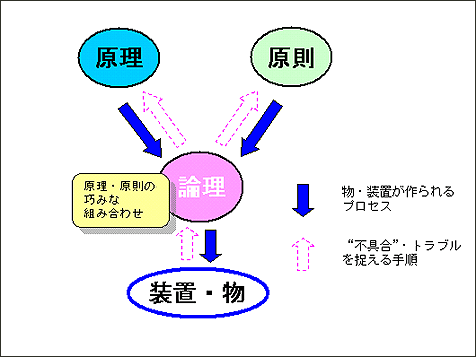
<図をクリックすると拡大表示します>
|
|
 |
 |
(4) |
“QAMM”実施の基本論理 |
|
“QAMM”では“不具合”を「品質」、「コスト」、「稼働率」(納期、迅速性等時間要素を含む)の3大要素に集約して取り扱います。
ほとんどの“不具合”は3大要素集約できます。無理にでも、“不具合”課題がどの要素に主に関係しているかを決めてみて下さい。
初めは無茶と感じても、限定できなかったことが、マネージメントの曖昧さであったことに気が付いて戴ける筈です。
今日、多くの課題は、「品質」が原因となるでしょう。しかし「品質」と言う定義こそ最も曖昧です。一つの「製品」が「商品」になると顧客による
要求品質は「千差万別」になります。ですから「品質」を直接的にマネージメントする固有の技術はありません。
「品質」のマネージメントに関係する要素は「コスト」、「稼働率」(納期、迅速性等時間要素を含む)です。
この二つの要素が「千差万別」の要求[顧客満足(CS)]を解決する具体的な手段です。お客さんの要求は “安くて良い物”、“欲しいもの直ぐに”が代表的です。
供給側から見ると「品質」/「コスト」、「品質」/「稼働率」の関係はネガティブです。
この“嫌な”ことを処理するのがマネージメントです。(この仕事の嫌な人はマネージャーをやめましょう)
この宝島を制した者が“勝者”です。
マネージャーはお金を“人”か“装置”或は双方に按配して使う方法を考えます。
但し如何に少なくするかが使命です。
このマネージメントは普遍ではありません。お客さんは生き物です。又、競争相手も生き物です。今日のマネージメントは明日は通用しないかも知れません。
何時も「品質」、「コスト」、「稼働率」(納期、迅速性等時間要素を含む)の3大要素の重点思考と日々の変更が必要なのです。
|
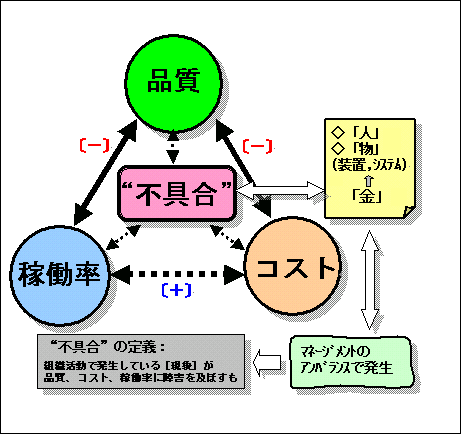
“不具合”発生の基本要素の相互関係
|
|
 |
 |
(5) |
“QAMM”実践フロー |
|
|
|
 |
 |
a |
“不具合”収集
“不具合”の商品、方法、生産工程等の発生したあるいは新規のテーマに関係している環境、工程の“不具合”を【条件設定をしないで】“困っている”ことを複数の人によって摘出する。
収集に当たっては、“困ったこと”を「現象」として捉え、“邪心”を拝して、「1事項」に4つ以上の“不具合”意見を抽出する。 |
b |
“不具合”の分類と個別仕分けと行程特性診断 |
|
収集した同類摘出をグループ化する。
“不具合”をマネージメントの改善課題視点で個別“不具合”を「“不具合”診断表」のマトリックスに従い該当箇所にマークを付ける。マークを各欄毎に集計する。
この集計から“不具合”プロセスの特性を診断。
重大“不具合”要因を“複合起因解析”で原因要素を確定する。
包装工程のオペレータの配置理由の“不具合”を「設備起因」、「人手起因」、「分類不明」に分けての調査した事例を【図】に示した。
|
|
c |
“複合起因解析”
“不具合”の定義を「品質」、「コスト」、「稼働率」の1つもしくは複数を決めて次の手順を変えずに厳密に解析をする
<0> 発生現象理解 <1> 関連部位の列挙 <2> “不具合”に関連する部位の選択
<3> “不具合”現象の関連原理の列挙 <4> 発生原理の解析/検証 <5>
改善(制御)策の技術開発/実施 |
|
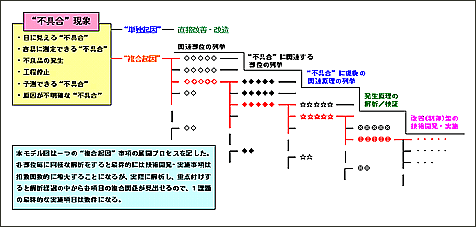
<図をクリックすると拡大表示します> |
d |
“発生源解析”
“不具合”の発生メカニズムを「原理」、「原則」と「論理」が物、装置にどのように展開されているかの検証方法
→ (3)“QAMM”の基本論理を参照して下さい |
e |
1%理論
“不具合”の発生を[1~0.1%]と[0.01%~]の発生確率に分けて解析して診ると発生メカニズムの特性に相違が発見できる。
前者は単独起因、後者は2つ以上発生要素が重なった場合に起こる複合起因である。
単独起因の“不具合”の改善は当面の“損害”は大きいが社会的問題にはならない。
一目見て“不具合”が分かるようであったり、お客さんが容易に発見できるような“不具合品”は売れないから、市場から自然淘汰される。しかし、発生確率の低い“不具合”はマネージメントからも漏れることが多く、件数は少なくとも、重大“不具合”に成ることが多いので格別の考慮が必要である。
“QAMM”では発生確率の低い“不具合”は“1%”程度の「非不具合」の重なりで発生すると定義。
発生確率が低いものは、関連要素が3つ以上関与することもある。
“QAMM”の詳細な展開で23件の関連要素を管理して、99.999%の稼働率の保証を達成した事例もある。関連要素の摘出のための基本論理、究明は“複合起因解析”により確定する。
|
|
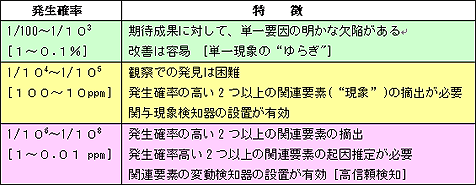
<図をクリックすると拡大表示します> |
f |
確率発生防御設計
“発生確率防御設計”は“1%”理論、“複合起因解析”の適用で摘出された“不具合”要素を設計に反映する際に要素の発生確率と“不具合”発生確率を推定し、改善効果を事前に評価し、設備やシステムの基本設計に反映する手法です。
【図】に示した事例はボトル充填における充填ノズルの挿入ミスの発生確率を推定したものである。
この例では99.7%の良好条件である。
この結果を実設備に反映したら、1000回に3回の挿入不良の発生は“不具合”と定義しないマネージメントが必要である。更に信頼性を高める場合には“不具合”の発生要素の各々のバラツキの“複合起因解析”を行いバラツキの発生原因を更に追究制御すればよい。
“QAMM”では定義された“不具合”の発生防御策はその構成要因が発見できれば6σ以上のマネージメントも可能である。
“不具合”検査装置が多く開発され市場に出回っているが、最終的には“不具合”の検査装置の信頼性の保証は極めて低いものであることが理解できよう。“不具合”発生要素の検知を行えば、0.1%の信頼性の廉価方法で“高信頼”“不具合”発生防御が可能になる。
|
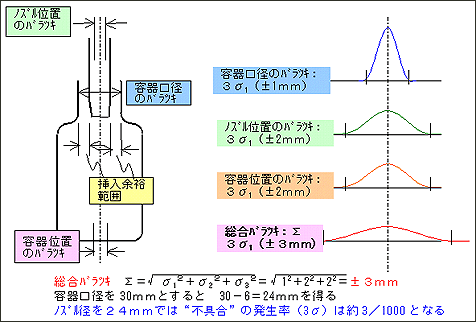
<図をクリックすると拡大表示します> |
|
 |
 |
(7) |
"QAMM"実施事例 |
|
“QAMM”の展開で顕著成果を挙げた事例項目;
・高速包装ラインの無人化の設計/建設/稼動
・介添え不要化包装ラインの設計/建設/稼動
・印刷工場のリードタイムの短縮化
・商事会社の不採算理由の究明
・誤出荷原因の究明
・ヒートシール“不具合”の原因究明と改善
ノウハウを汎用化した「溶着面温度測定法」;“MTMS”に展開 |
|